The fundamental design of these specialized valves centres on maintaining consistent material flow while preserving system pressure. The engineering process involves precise calculations and rigorous testing to ensure optimal performance. When examining industrial processing systems, air rotary valves emerge as critical components that regulate material discharge while maintaining pressure equilibrium.
Primary design considerations
- Material selection and durability
The construction incorporates high-grade metals and advanced coatings that withstand continuous operation. Each component undergoes strict quality control to guarantee seamless functionality and extended service life. The rotor assembly, housing, and end plates receive particular attention during the design phase.
- Clearance optimization
Engineers meticulously calculate the clearances between rotating and stationary components. These measurements directly impact the valve’s ability to maintain pressure differentials while preventing material leakage. The rotor-to-housing clearance specifically influences overall system efficiency.
Precise rotor configuration – Balancing efficiency with pressure control
The rotor design significantly influences the valve’s performance. Multiple pocket configurations distribute material evenly while maintaining consistent airflow. air rotary valveutilize specialized vane arrangements that optimize material handling capacity without compromising pressure maintenance.
Sealing mechanisms and pressure management
Advanced sealing technologies prevent air leakage between valve chambers. The strategic placement of seals and careful material selection ensure reliable operation under varying pressure conditions. Multiple seal types work together to maintain system integrity.
Integration of monitoring systems
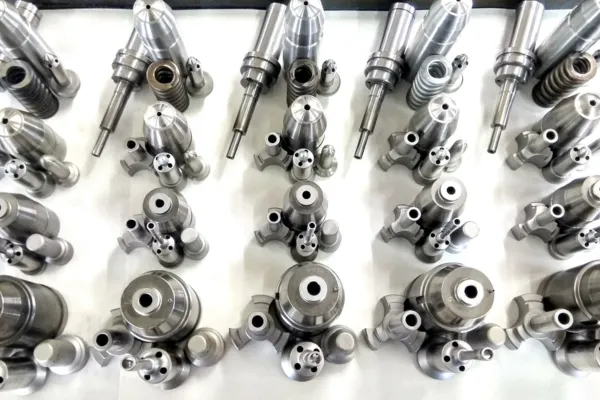
Modern designs incorporate sensors and monitoring equipment to track performance metrics. These systems provide real-time data about rotation speed, pressure differences, and material flow rates. The integration of digital monitoring enhances operational control and maintenance planning.
Safety features and fail-safe mechanisms
Comprehensive safety features protect both equipment and operators. Emergency shutdown systems respond instantly to irregular pressure conditions. The air rotary valve design includes multiple redundant safety measures that prevent system damage during unexpected events.
Customization capabilities
Manufacturing processes allow for application-specific modifications. The valve dimensions, rotor configurations, and material specifications adapt to unique operational requirements. This flexibility ensures optimal performance across diverse industrial applications.
Maintenance accessibility
The design prioritizes easy access to critical components. Regular maintenance procedures require minimal system disruption. Quick-release features and modular construction simplify inspection and parts replacement.
Performance optimization features
- Automated control systems
Smart controls adjust operation parameters based on real-time conditions. These systems optimize rotation speeds and material flow rates automatically. Integration with facility control systems ensures coordinated operation.
- Energy efficiency elements
The design minimizes power consumption through balanced loading and precise machining. Efficient motor selection and drive systems reduce operational costs. Energy-saving features maintain performance while optimizing resource utilization.
Summary of key design elements
The successful design of these valves requires careful attention to multiple factors:
- Precision engineering of all components
- Integration of advanced sealing systems
- Implementation of smart control mechanisms
- Focus on maintenance accessibility
- Incorporation of safety features
- Optimization of energy consumption
The approach to valve design ensures reliable performance across various industrial applications. Each element works together to maintain system efficiency while managing pressure differentials effectively. Regular assessment and updates to design specifications keep pace with evolving industry requirements and technological advances.
The intricate design process behind these valves demonstrates the complexity of industrial flow control systems. Components serve particular purposes to ensure optimal performance. The continuous evolution of design principles ensures these critical components meet future industrial challenges effectively.